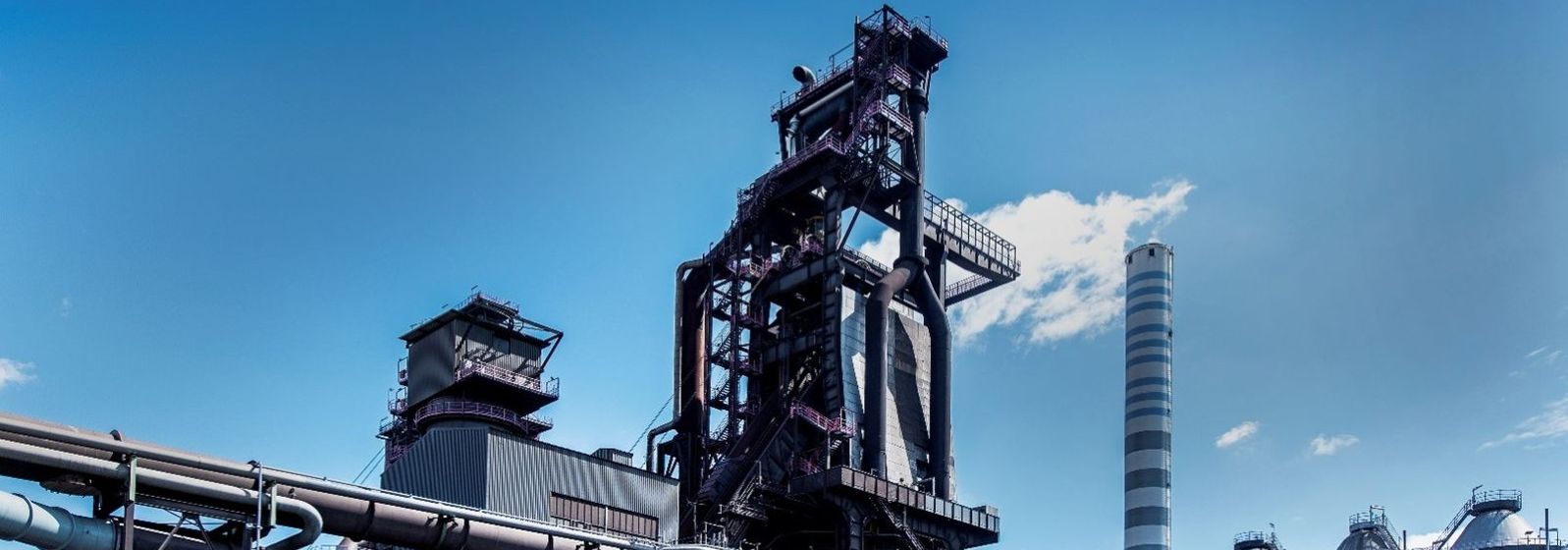
Der Weg in die industrielle Praxis
Reallabor der Energiewende H2Stahl bringt Wasserstoff in die Stahlindustrie
Wie lässt sich Stahl klimafreundlich erzeugen und welche Technologien können die Transformation der Branche beschleunigen? Das wollen die Projektpartner im Reallabor der Energiewende H2Stahl herausfinden.
Entsprechend der deutschen Klimaziele strebt auch die Stahlindustrie die Klimaneutralität bis 2045 an. Das Problem: Führende Unternehmen wie Thyssenkrupp Steel verursachen mit ihren Hochöfen derzeit noch bis zu 50.000 Tonnen CO2 pro Tag – das entspricht in etwa dem jährlichen Ausstoß von 30 Autos. Für die Dekarbonisierung muss demnach ein umfassender Lösungsweg gefunden werden. Eine Möglichkeit bietet etwa die Umstellung von fossilen Energieträgern auf Wasserstoff.
Grüner Wasserstoff ist der Schlüssel für eine erfolgreiche Transformation
Rund 30 Prozent der industriellen CO2-Emissionen in Deutschland entfallen auf die Stahlproduktion. Entsprechend hoch sind die Erwartungen an das Einsparpotenzial der Branche. Moderne Hochöfen arbeiten heute schon sehr effizient – deshalb lässt sich die CO2-Bilanz bei der klassischen Produktion mit kohlenstoffhaltigen Reduktionsmitteln kaum noch verbessern. Das liegt daran, dass bei der Reduktion von Eisenerz zu Roheisen zwangsläufig CO2 entsteht: Der Sauerstoff im Erz verbindet sich mit dem Kohlenstoff aus der Kohle.
Um die Emissionen grundlegend zu senken, ist ein Technologiewechsel erforderlich – und das bei laufender Produktion. Der nächste Schritt ist damit unweigerlich, auf ein kohlenstofffreies und damit klimafreundlicheres Reduktionsmittel umzusteigen. Als Schlüssel gilt hier grüner Wasserstoff. Im Reallabor H2Stahl erproben die Projektpartner Thyssenkrupp Steel und das VDEh-Betriebsforschungsinstitut (BFI), wie der Umstieg auf nachhaltige Technologien in der Stahlherstellung gelingen kann.
Direktreduktion als Weg zur CO2-Neutralität
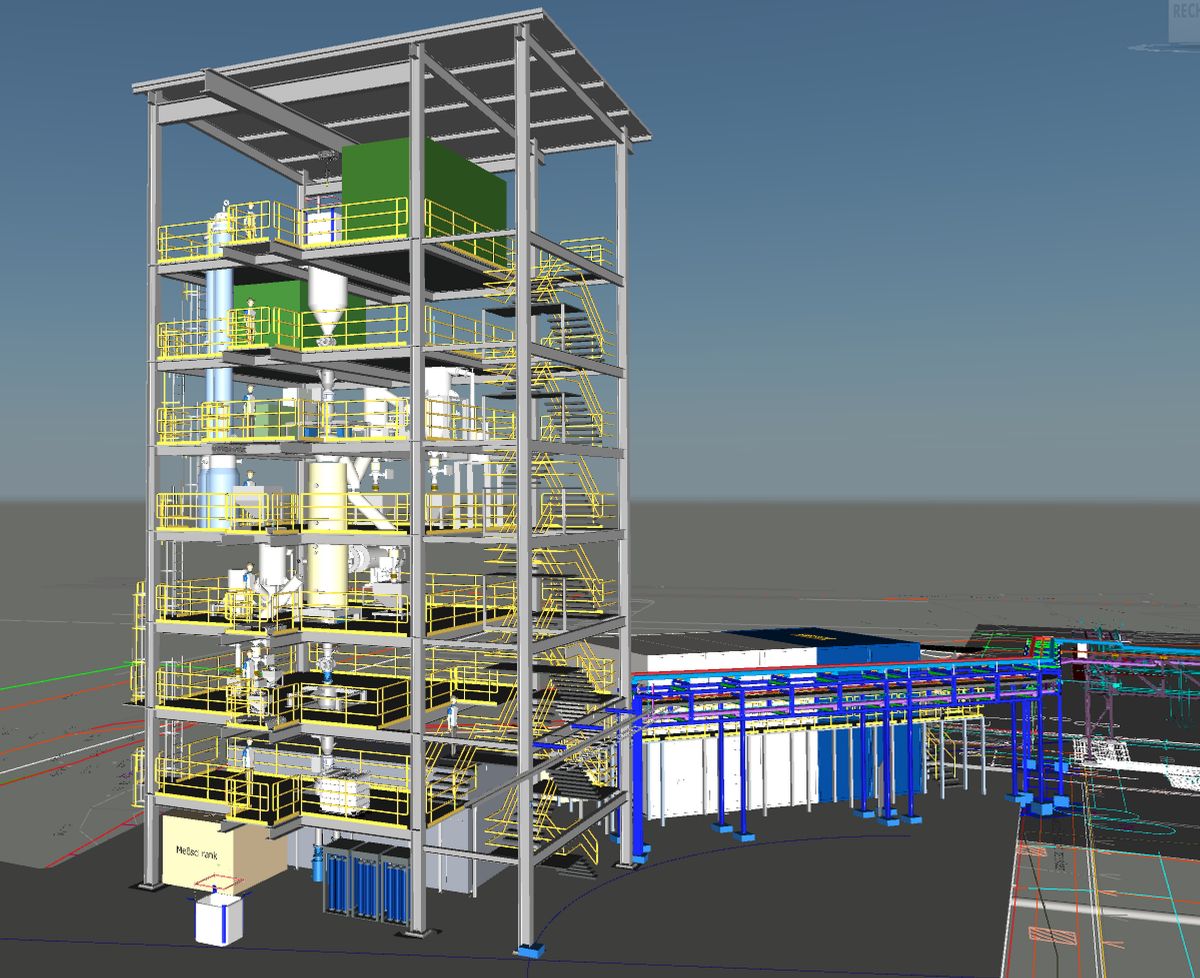
Ein zentrales Element der Transformation ist die sogenannte Direktreduktion (DR). Dabei wird Eisenerz nicht im Hochofen mit Kohle geschmolzen, sondern mithilfe von Wasserstoff reduziert. Diese Methode hat das Potenzial, langfristig große Mengen CO2 einzusparen. Im Projekt H2Stahl wird untersucht, wie sich diese Technik weiterentwickeln lässt – zunächst mit wasserstoffreichen Gasen als Übergangslösung, später vollständig mit grünem Wasserstoff.
„Die Direktreduktion mit verschiedenen Gasen ist noch nicht ausgereift genug, um sie an bestehenden Anlagen einzusetzen. Daher gilt es, die einzelnen Gasgemische und ihr Verhalten im Rahmen des Projektes in einer DR-Versuchsanlage weiter zu erforschen“ sagt Michael Hensmann, Abteilungsleiter für Ressourcentechnologie Einsatzstoffe beim BFI. Ziel des Projekts ist es daher, in einer speziellen Versuchsanlage das Verhalten unterschiedlicher Gasgemische – Wasserstoff, Erdgas und wasserstoffhaltige Prozessgase – zu analysieren. Dabei kommen eisenoxidhaltige Materialien wie Pellets, Stückerze oder industrielle Reststoffe zum Einsatz.
Die gewonnenen Erkenntnisse sollen helfen, die gesamte Roheisenproduktion am Duisburger Standort zukünftig auf die Direktreduktion umzustellen. Ein großer Vorteil: Das Verfahren ist flexibel und lässt sich mit wechselnden Anteilen Wasserstoff betreiben. Außerdem ist sie mit einem Großteil der bestehenden Infrastruktur kompatibel: Bei der Direktreduktion entsteht zunächst Eisenschwamm, der dann eingeschmolzen wird und mit derselben Technik weiterverarbeitet werden kann, die auch bei flüssigem Roheisen aus dem klassischen Hochofen zum Einsatz kommt. Da sich beim DR-Verfahren verschiedene Gase flexibel einsetzen lassen, entkoppelt dieses die Stahlherstellung ein Stück weit vom Wasserstoffmarkt. Somit ist die Produktion nicht vollständig von grünem Wasserstoff abhängig.
Die Transformation einer ganzen Branche vorantreiben
H2Stahl will die schwierige Phase zwischen der Technologieentwicklung und der Marktdurchdringung beschleunigen. „Wasserstoff wird von zentraler Bedeutung für die Stahlproduktion in Deutschland sein“ , sagt Frank Ahrenhold, Leiter für nachhaltige Stahlerzeugung bei Thyssenkrupp Steel. „Die in H2Stahl errichtete Infrastruktur kann langfristig für die Transformation des Werkes zur Verfügung stehen und lässt sich für Untersuchungen zur Direktreduktion nutzen.“
Die in H2Stahl gewonnenen Erkenntnisse sind nicht nur für Duisburg relevant, sondern lassen sich auch auf andere Stahlwerke in Deutschland übertragen. Somit kann das Reallabor der Energiewende die schrittweise Transformation der gesamten Branche vorantreiben. Frank Ahrenhold betont: „Mit dem H2Stahl zeigen wir, dass wir die Transformation des europäischen Stahlstandorts weiter konsequent angehen. Wir schaffen die Kohle ab, nicht das Stahlwerk.“ (ks/mr)