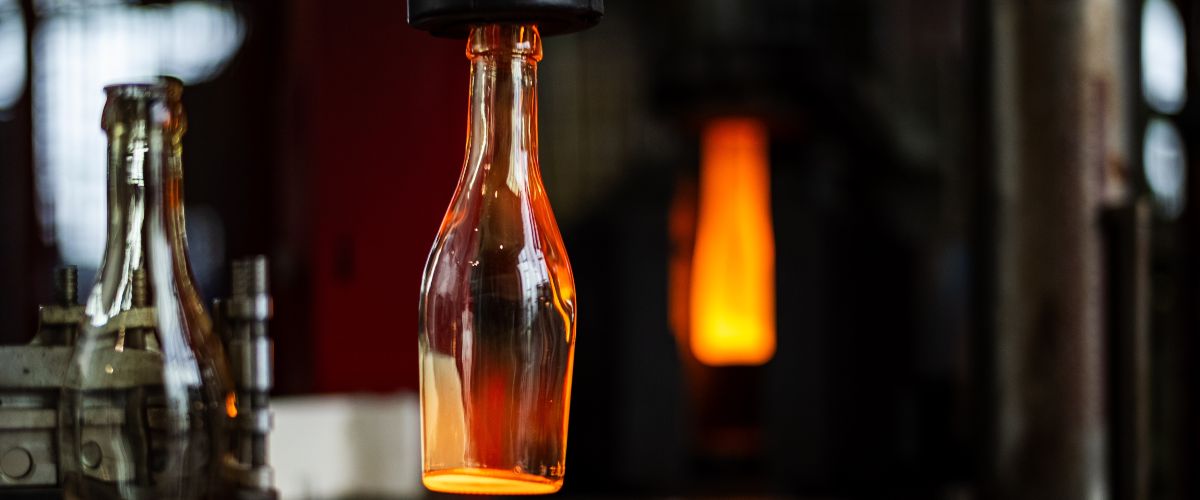
Dekarbonisierung der Prozessindustrie
Wasserstoff trifft Hochtemperatur: Stahl, Ziegel und Glas klimafreundlich produzieren
Die Forschungsprojekte ZeroCO₂-Glas, KLIMAZIEGPROD, Hybrid-FIRE und H₂-DisTherPro stehen für eine neue Generation industrieller Verfahren. Mithilfe von (grünem) Wasserstoff und Strom arbeiten Forschende daran, zentrale Prozesse der Glas-, Ziegel-, Keramik- und Stahlherstellung klimaneutral zu gestalten.
Die Herstellungsprozesse der genannten Produkte sind auf besonders hohe Temperaturen angewiesen – bisher werden diese vor allem durch fossile Energieträger wie Erdgas oder Öl erzeugt. Damit die Umstellung auf grünen Wasserstoff und regenerativ gewonnenen Strom gelingt, sind noch einige Anforderungen zu erfüllen. Ein kurzer Einblick in die vier Forschungsprojekte zeigt, welchen Herausforderungen das sind und woran die Wissenschaftsteams konkret forschen.
Emissionsfreie Glasherstellung: ZeroCO₂-Glas entwickelt neue Schmelzwanne
Ob Marmeladengläser, Gurken im Glas oder die klassische Milchflasche – Behälter und Konserven aus Glas werden im Alltag in großen Mengen genutzt. Im Projekt ZeroCO₂-Glas arbeitet ein Forschungsteam an einem emissionsfreien Schmelzprozess am Beispiel der Flaschenproduktion.
Anders als in der herkömmlichen Glasherstellung sollen künftig carbonatfreie Rohstoffe eingesetzt werden – bislang wird das Glas aus einem Gemenge aus Sand und Rohstoffen wie Calciumcarbonat und Natrium-carbonat produziert. Weiterhin entwickeln die Forschenden eine neuartige Schmelzwanne, die flexibel mit wechselnden Anteilen Strom und mit einer Wasserstoff-Sauerstoff-Verbrennung betrieben werden kann. Dies soll ermöglichen, auf fossile Brennstoffe wie das bisher eingesetzte Erdgas zu verzichten. Wichtig ist, mehr Erkenntnisse über den Einfluss der wasserstoffhaltigen Atmosphäre auf die Glasherstellung zu gewinnen.
Dabei sind etwa Themen wie die andersartigen Flammeigenschaften, der vermehrte Anfall von Wasserdampf und Veränderungen im Abgas zu berücksichtigen, die sowohl die Glasqualität als auch Schmelzwanne und Ofenmauerung beeinflussen. Ferner untersuchen die Forschenden auch, wie sich die neue Glaszusammensetzung auf die Formgebung und das finale Produkt auswirkt.
Bei der Entwicklung der neuen Schmelzwanne schauen sich die Wissenschaftlerinnen und Wissenschaftler auch das Design näher an, um die Gemengeeinlage zu optimieren. Ziel ist, dass die Rohstoffe zu Beginn des Prozesses weniger Feuchtigkeit aufweisen müssen, um Staub vermeiden zu können. Damit könnte auch die Energieeffizienz weiter gesteigert werden.
Ziel der Forschenden ist es, in ZeroCO2-Glas einen Demonstrator der Glasschmelzwanne zu entwickeln. Dieser soll rund 2,4 Tonnen Glas pro Tag herstellen – ein wichtiger Schritt in Richtung CO₂-freier Glasproduktion.
Ziegel klimaneutral brennen: KLIMAZIEGPROD testet Wasserstoff im Tunnelofen
Die Ziegelindustrie verursacht in Deutschland jährlich rund 1,74 Millionen Tonnen CO₂. Eine vollständige Substitution von Erdgas als Brennstoff – etwa durch regenativ gewonnenen Wasserstoff – würde einen CO2-freien Brennprozess ermöglichen und potenziell fast 1,09 Millionen Tonnen des klimaschädlichen Gases vermeiden.
Im Forschungsprojekt KLIMAZIEGPROD rüsten Forschende eine Brennergruppe eines bestehenden Tunnelofens auf den Betrieb mit bis zu 100 Prozent Wasserstoff um und untersuchen die im Pilotbetrieb hergestellten Ziegelprodukte. Ihr Ziel ist es, potenzielle Wechselwirkungen und Einflüsse auf den Brennprozess und die Qualität der keramischen Werkstoffe zu identifizieren und ein praxistaugliches Konzept für einen möglichst kontinuierlichen Ofenbetrieb für grobkeramische Baustoffe wie Dachziegel oder Klinker abzuleiten.
Durch den Wasserstoff entsteht eine wasserdampfhaltige Ofenatmosphäre, die es ermöglicht, die Brenntemperatur abzusenken. Erste Versuche zeigen, dass Hintermauerziegel, die mit Wasserstoff gebrannt wurden, eine rund 15 Prozent höhere Druckfestigkeit aufweisen als Ziegel, die mit Erdgas bei gleicher Temperatur gebrannt wurden. Ebenso verringert sich die Brennerluftmenge, da Wasserstoff im Vergleich zu Erdgas weniger Luft für die Verbrennung benötigt. Dadurch muss weniger Luft im Ofenraum erwärmt werden. Beide Aspekte führen dazu, dass mit dem Einsatz von Wasserstoff zusätzlich Energie eingespart werden kann. Bei Versuchen in einem mit Erdgas und Wasserstoff beheizbaren Kammerofen, haben die Wasserstoffbrände etwa sieben Prozent weniger Energie benötigt.
Für die industrielle Praxis ist insbesondere der Nachweis positiver Einflüsse auf den Brennprozess gefragt. Zeitgleich ist es in der Branche wichtig, weiterhin auf Kundenwünsche eingehen zu können – etwa bezüglich der Farbgebung der Ziegel von Anthrazit bis „Ziegelrot“. Im Forschungsprojekt KLIMAZIEGPROD achtet das Forschungsteam daher auch auf diese Parameter im Brennprozess. Nach Projektende ist die Umsetzung der Ergebnisse in die Praxis bei einem der Projektpartner geplant. Ebenso streben die Forschenden einen brancheninternen und branchenübergreifenden Transfer auf weitere Baustoffe an.
Hybrid-FIRE: CO₂-arme Hybrid-Ofentechnologie für Keramik und Stahl
Bei der Herstellung von Keramiken macht der Sinterprozess rund 70 Prozent des gesamten Energieverbrauchs aus. Auch andere Branchen wie die Zementindustrie, die Kalkbrennerei und die Eisen- und Stahlerzeugung teilen die Herausforderung, aufgrund der vielen Thermoprozesse große Mengen Energie zu verbrauchen und viel CO2 auszustoßen.
Im Forschungsprojekt Hybrid-FIRE schaut sich ein Team daher den Brennprozess von gleich zwei Produktgruppen an. Die Forschenden entwickeln einen Hybridofen für keramische Massenerzeugnisse und das Stahlschmelzen, der eine weitgehend CO2-freie Behandlung ermöglicht. Grundlage sollen umweltfreundlich erzeugter Wasserstoff und Elektroenergie sein. Der Wasserstoff ersetzt das bislang genutzte Erdgas in einem herkömmlichen Brenner, der nun zusätzlich mit einem oder mehreren Mikrowellenplasmabrennern kombiniert wird.
Während des Projekts konzipieren und bauen die Forschenden dazu einen Demonstrator-Ofen, den sie anschließend umfangreich mit den verschiedenen Produktgruppen testen. Die gewonnenen Erkenntnisse sollen zudem bei zwei Projektpartnern im Bereich der Feuerfestherstellung und der Stahlgießerei unter industriellen Bedingungen erprobt werden. Sie erwarten, dass die Hybrid-Technologie die Energieeffizienz in beiden Bereichen um mindestens 15 Prozent steigern kann.
Auch in diesem Projekt zählt die veränderte oder auch schwankende Menge an Wasserdampf beziehungsweise die wasserstoffhaltige Ofenatmosphäre zu den großen Herausforderungen. Daher untersuchen die Forschenden, welchen Einfluss dies auf die Gesamteffizienz des thermischen Prozesses hat und in wieweit dieser angepasst werden muss, damit die im Ofen eingesetzte feuerfeste Auskleidung und die Werkstücke thermoschockmäßig geschont werden. Geplant ist, dass der Wasserstoffbrenner das Vorheizen übernimmt und der oder die Mikrowellenplasmabrenner das eigentliche Sintern beziehungsweise Schmelzen ermöglichen.
Ein großer Vorteil für den späteren Praxistransfer ergibt sich dadurch, dass die Mikrowellenplasmabrenner an bereits vorhandenen Anlagen angebracht werden können und damit eine hohe Kompatibilität aufweisen. Zudem besitzen sie eine flexible, steuerbare Brennerfackel mit hohem Wirkungsgrad. Bei deutschlandweit etwa 770.000 Tonnen hergestellter keramischer Erzeugnisse pro Jahr, dürften die Energie- und CO2-Ein-sparungen entsprechend hoch ausfallen. Ebenso sieht es in der Stahlherstellung aus - hochgerechnet auf ganz Deutschland haben die Forschenden eine Energieeinsparung von über drei Gigawattstunden berechnet.
H₂-DisTherPro: Verpackungsstahl mit grünem Wasserstoff herstellen
Bei der Herstellung von Konservendosen durchläuft Verpackungsstahl mehrere Wärmebehandlungen. Besonders energieintensiv ist das rekristallisierende Glühen, das meist mit Erdgas erfolgt. Im Projekt H₂-DisTherPro entwickelt ein Forschungsteam ein Konzept, um diesen Prozess schrittweise auf Wasserstoff umzustellen. Dabei untersuchen Forschende, wie viel Wasserstoff dem Erdgas beigefügt werden kann, ohne konstruktive Änderungen an der Anlage vornehmen zu müssen und was entsprechend notwendig ist, um den Betrieb vollständig mit Wasserstoff zu ermöglichen.
Insbesondere die physikalischen und verbrennungstechnischen Eigenschaften von Wasserstoff gegenüber Erdgas schauen sich die Forschenden in H2DisTherPro genauer an. Hierbei geht es etwa um Anforderungen an die zuliefernden Rohrleitungen, nötige Gasmengen und ausreichende Gasdrücke sowie veränderte verbrennungstechnische Eigenschaften, wie Flammengeschwindigkeit und Flammentemperatur, die sich auf die Brenner und Wärmeübertragung auswirken. Auch hier ist der höhere Wasserdampf-Anteil im Verbrennungsgas Thema, da sich der Wärmeübergang im Prozess dadurch verändert. Herausforderungen neben der einwandfreien Prozessführung bestehen zudem darin, die gewünschte Produktqualität gewährleisten zu können.
Mit dem Forschungsprojekt H2DisTherPro gewinnt das Team wichtige Erkenntnisse, um diskontinuierliche Thermoprozessanlagen zukünftig CO2-ärmer zu betreiben und die Stahlindustrie auf eine klimafreundliche Alternative umzustellen. So schätzt das Wissenschaftsteam, dass ein vollständiger Umstieg des Haubenglühverfahrens auf grünen Wasserstoff neben der Senkung von CO2-Emissionen bundesweit jährlich fast 50 Gigawattstunden Energie einsparen könnte.
Wasserstoff in der Thermoprozesstechnik: Gemeinsame Herausforderungen, übertragbare Lösungen
Die vier vorgestellten Projekte zeigen: grüner Wasserstoff und regenerativ gewonnener Strom spielen eine Schlüsselrolle für eine klimafreundliche Prozessindustrie. Zwar sind die Produkte vielfältig und die Prozesse im Detail unterschiedlich, doch die Herausforderungen und Lösungswege industrieller Thermoprozesse ähneln sich: veränderte Ofenatmosphären, Materialverträglichkeit, Effizienzfragen und Prozessstabilität. An diesen Schnittstellen zwischen Innovation und industrieller Machbarkeit setzen die Forschungsprojekte an und liefern übertragbare Lösungen. So entsteht nicht nur neues Wissen, sondern eine Grundlage für eine skalierbare, klimafreundliche Industrieproduktion. (ln)