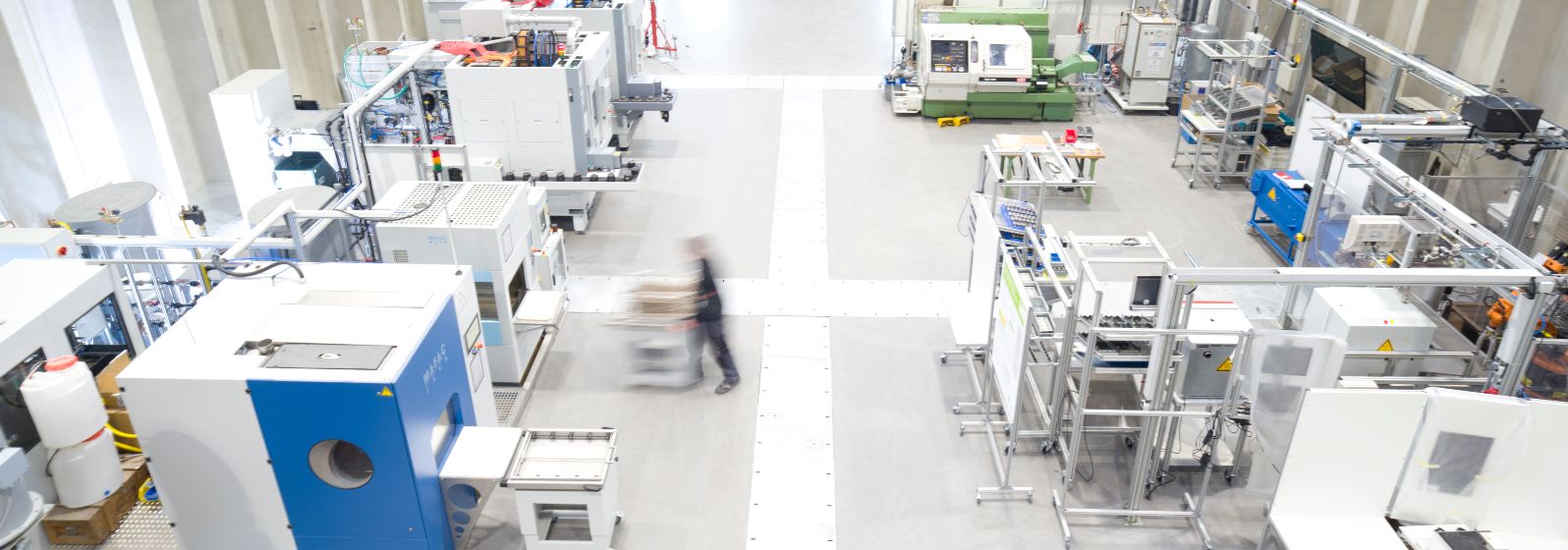
Von der Forschung in die Praxis
Wir haben bewiesen: Effizienzsteigerungen sind möglich
Dr. Bernd Müller Mission Energiesystem 2045, Mission Stromwende 2045, Mission Transfer, Mission Wärmewende 2045
Wie können die Anlagen und die Infrastruktur einer Fabrik effizienter werden? Mit dieser Frage ist vor fast 10 Jahren das Forschungsprojekt ETA-Fabrik gestartet. Heute sind die Ergebnisse beim damaligen Projektpartner Bosch Rexroth deutlich zu sehen. Wie Effizienzmaßnahmen nun zum Betriebsalltag gehören, erklärt Dr. Bernd Müller.
2013 ist mit der ETA-Fabrik ein groß angelegtes Forschungsprojekt zur Energieeffizienz von Anlagen und Infrastruktur in Industrie und Gewerbe gestartet. Auf einem Gelände der TU Darmstadt wurde dafür eine Forschungsfabrik gebaut, in der Wissenschaftlerinnen und Wissenschaftler gemeinsam mit insgesamt 37 Industriepartnern an Effizienztechnologien geforscht und entwickelt haben.
Einer dieser Industriepartner war Bosch Rexroth. Der Hersteller für Antriebs- und Steuerungstechnik hat in der ETA-Fabrik eine eigene Produktionskette auf den Prüfstand gestellt. Diese wurde originalgetreu nachgebaut und mit verschiedenen Effizienzmaßnahmen optimiert. Im firmeneigenen Projekt GoGreen werden diese Maßnahmen bis heute weiterentwickelt und angewendet. Bis 2021 konnte Bosch Rexroth damit pro Million Euro Umsatz über 40 Prozent Energie einsparen.
Bernd Müller hat die Abteilung GoGreen mit aufgebaut. Im Video-Interview spricht er darüber, wie sein Team und er diese Ziele erreicht haben, was nötig ist, damit auch Mitarbeitende beim Energiemanagement mitziehen und warum Konkurrenzdenken beim Thema Nachhaltigkeit nicht an erster Stelle steht.
Das Interview führten Kim Statzner und Leona Niemeyer, Wissenschaftsjournalistinnen beim Projektträger Jülich, im Rahmen des Kongresses Energieeffizienzforschung für Industrie und Gewerbe im Mai 2022.
Videoschnitt: Kim Statzner
Voice-Over: Wie kann die Energiewende in der Industrie vorangebracht werden? Was muss passieren, damit Forschungsergebnisse schneller in die Praxis kommen? Und wie kann die Förderpolitik dabei helfen? Darüber haben Expertinnen und Experten beim Kongress Energieeffizienzforschung für Industrie und Gewerbe in Berlin gesprochen. Einer von ihnen ist Bernd Müller. Er arbeitet bei Bosch Rexroth, einem Hersteller für Antriebs- und Steuerungstechnik, und hat dort die Abteilung GoGreen eingerichtet.
Diese arbeitet daran, die Energieversorgung, die Infrastruktur und die Produktionsprozesse des Unternehmens effizienter und nachhaltiger zu gestalten. Dazu hat das Team unter anderem an der ETA-Fabrik mitgewirkt, einem vom Bundesministerium für Wirtschaft und Klimaschutz geförderten Forschungsvorhaben. In der Modell-Fabrik haben die Projektpartner eine Produktionskette von Bosch Rexroth originalgetreu nachgebaut und effizienter gestaltet. Inzwischen ist das ursprüngliche geförderte Vorhaben abgeschlossen. Die Arbeiten im Projekt GoGreen laufen jedoch weiter.Heute schult das Team auch andere Unternehmen zum Thema Energieeffizienz. Wir haben Bernd Müller am Rande des Kongresses getroffen und genauer nachgefragt.
Wie ist die Idee für GoGreen entstanden?
Müller: 2009 hatte die Bosch Rexroth AG sich selbst verpflichtet, die Kyoto Ziele zu erreichen und den relativen CO2-Ausstoß um 20 Prozent zu senken. Die Rexroth AG als Anbieter von Energieeffizienz-Lösungen war natürlich auch daran interessiert, dass wir diese Reduktionen nicht nur durch Einkauf von Grünstrom oder sonstige Maßnahmen reduzieren, sondern dass wir darüber hinaus auch zeigen, was im Maschinenbau möglich ist, um Energieeffizienz zu steigern.
Wie haben Sie das Projekt umgesetzt?
Müller: Wir hatten sofort gesehen, dass die Werke es alleine nicht schaffen können, auch wenn sie motiviert waren und das Ziel alle angesprochen hatte. Es war klar, dass die Werke Unterstützung brauchen und so hatten wir eine Zentralstelle eingerichtet und besetzt. Diese Zentralstelle GoGreen hatte das Projekt angenommen. Die Besetzung ist mit sieben Mitarbeitern erfolgt. Gleichzeitig haben wir auch in jedem Werk einen Energiemanager eingestellt. Die haben die Methodik entwickelt, die Analysen gemacht, das Reporting, aber auch in Verbundforschungsprojekten mitgearbeitet, wie die ETA-Fabrik an der TU Darmstadt.
Voice-Over: Die ETA-Fabrik wurde 2013 im Rahmen eines Forschungsprojektes auf einem Gelände der TU Darmstadt gebaut. Bei dem Projekt haben insgesamt 37 Industriepartner mitgearbeitet, unter anderem Bosch Rexroth. Ihr Ziel war es, den Energieverbrauch von Anlagen und Infrastruktur zu senken. Das Projekt ist seit 2018 abgeschlossen. Seitdem führen verschiedene Folgeprojekte die Forschung in der Fabrik weiter. Mehr dazu in der Infobox.
Wie lassen sich alle Mitarbeitenden bei so einem Projekt mitnehmen?
Müller: Wir hatten eine einwöchige Schulung aufgebaut für alle Energiemanager, damit sie die Logiken der Analyse und auch die Hebel zur Energiesenkung oder -effizienzsteigerung erlernen. Und das war sehr, sehr wichtig, nicht nur in der Wissensvermittlung, sondern auch in der Teambildung. Wenn sie weltweit dann die Energiemanager zusammenbringen, dann bestärken sie sich auch gegenseitig. Denn es ist eine unheimlich schwierige Aufgabe, das Verhalten von Menschen zu verändern.
Jemand geht aus der Produktion raus oder die Produktion ist unterbrochen, weil Stückzahl fehlt und er muss die Maschine abschalten. Normalerweise interessiert ihn das in dem Moment nicht. Aber das Verhalten so zu ändern, dass er lernt Abschalt-Management spielt eine große Rolle – das war uns sehr wichtig. Geholfen hat uns natürlich auch die Methodik „Continuous Improvement“, mit der wir Bestände oder Ruhezeiten reduziert hatten.
Insofern hatten wir auch Plattformen, wie wir in Lernstattrunden – wir nennen es Lernstatt – Mitarbeiter in ihrem Verhalten auch befähigen konnten und auch Erfolgsmomente mitgeben konnten. Das war auch wichtig, dass wir sehr schnell frühe Erfolge hatten.
Welche Wirkung hatten Ihre Erfolge bei GoGreen auf Ihre Wettbewerber?
Müller: Zahlreiche Kunden von Rexroth hatten unseren Vertrieb angesprochen. Wir bekamen Auszeichnungen. Dadurch hatten sie gesehen, welche Fortschritte wir hatten. Und wir haben in unsere internen Schulungen auch befreundete Unternehmen mit eingeladen. Wir haben auch ein Buch herausgegeben, wie wir im Projekt vorgegangen sind, welche Methoden und Techniken wir angewandt hatten. Und das geben wir sehr gerne auch an andere Unternehmen weiter.
Wie hoch ist die Bereitschaft, Wissen zu teilen und gibt es da kein Konkurrenzdenken?
Müller: Die Maßnahmen werden wir primär ergriffen durch Menschen in der Produktion. Das heißt, die haben gar keinen Wettbewerbs-Gedanken primär. Wir haben alle das gleiche Ziel: Jede CO2-Einsparung nützt jedem. Insofern sehen wir uns da gar nicht in der Konkurrenzsituation, sondern sind sehr, sehr offen mit den Lösungsansätzen, die wir entwickelt haben zur CO2-Reduktion.
Wie wichtig ist die Selbstverpflichtung von Unternehmen?
Müller: Sehr wichtig. Wenn man mal betrachtet, was so ein Werkleiter oder was Führungskräfte doch für enorme Anstrengungen unternehmen müssen: Die normalen Ziele Liefererfüllung, Bestandssituation, Qualitätsprobleme zu bearbeiten. Dann ist von unten betrachtet die Energieeffizienz ein C-Thema. A- und B-Themen, die kann die Führungskraft selber noch verfolgen, behandeln, unterstützen. Aber ein C-Thema ist ein Thema, das er delegieren muss.
Uns war aber klar: Wir mussten einen Stab von Leuten aufbauen, der dann in den Werken die Maßnahmen entwickelt, einführt und die Betroffenen allenfalls zu Beteiligten macht. Und ich bin froh, dass unser Mutterkonzern Bosch bis 2030 insgesamt ein Budget von einer Milliarde freigegeben hat für energieeffizienz-steigernde Maßnahmen. Das kommt auch daher, weil wir bewiesen haben, dass wir Effizienzsteigerungen vornehmen können und auch messbar gemacht haben.
Warum sind Verbundprojekte und Forschungsförderung trotzdem wichtig für Sie?
Müller: Wenn wir uns mal ansehen, von wem wir die Produktionseinrichtungen bekommen, die Anlagen: Dann sind es kleinere und mittelständische Unternehmen. Das sind nicht Großunternehmen – die Ofenbauer, die Reinigungsanlagen-Hersteller, das sind kleinere Unternehmen, die haben keine große zentrale Forschungsstelle. Und wenn man jetzt eine neue Entwicklung von denen möchte, dann brauchen die den Stand der Wissenschaft. Sie brauchen Zugang zu technischem Grundlagenwissen.
Wir haben in unserem Unternehmen natürlich auch eine zentrale Forschung. Wir konnten dort auch Wissen mit einbringen, aber es ist doch sehr wichtig, dass diese gefördert werden. Und in diesem Verbundforschungsvorhaben war es dann auch möglich, dass der Reinigungsanlagen-Hersteller mit dem Hersteller der Herdeanlage sprechen konnte und sie sehen konnten: Wie kann ich denn die Abwärme für die Reinigung nutzen?
Voice-Over: Aus dem ehemaligen Projekt ist inzwischen ein fester Bestandteil des Unternehmens geworden. Bis 2021 konnte Bosch Rexroth pro Million Euro Umsatz über 40 Prozent Energie einsparen. Dadurch und durch die Umstellung auf klimaneutrale Energieträger hat das Unternehmen seine CO2-Emissionen um rund 85 Prozent reduziert. Mehr Informationen zur ETA-Fabrik und zu GoGreen, der Forschungsförderung des BMWK und zu weiteren Projekten der angewandten Energieforschung gibt es in der Infobox.