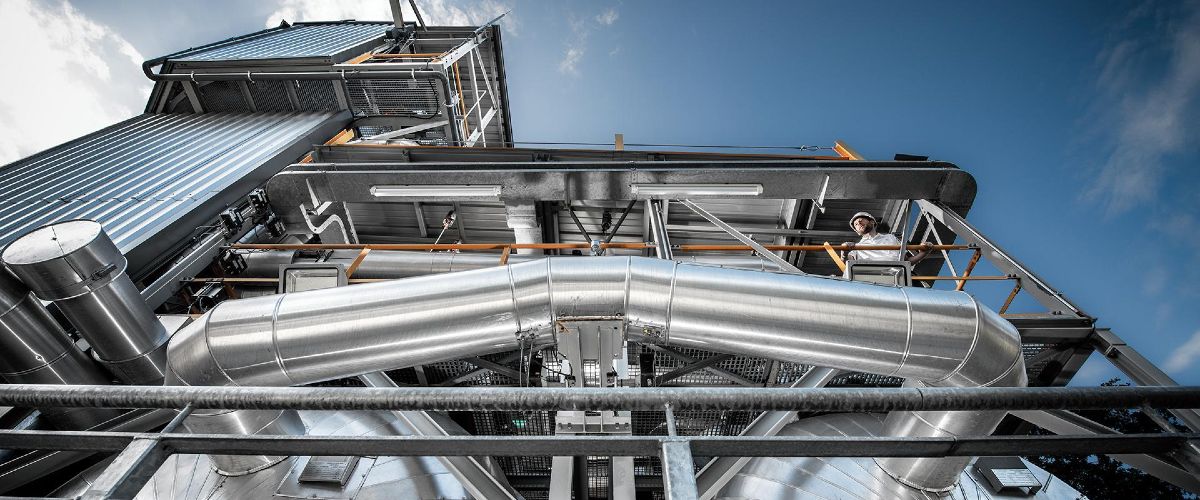
Solar thermal power plants
Reduce costs: Liquid salt storage with innovative storage material
Liquid salt is a popular heat transfer medium in high-temperature heat storage tanks. In order to reduce costs and thus open up further areas of application, part of the liquid salt is to be replaced. The team of scientists in the Newcline project is therefore researching a single-tank concept with heat-storing bricks.
Everyone knows it: The more ice cubes there are in a refreshing cola, the less caffeine drink there is in the glass. This principle has been adopted by scientists at the German Aerospace Center (DLR) and the Kraftblock company. They are researching heat-storing moulded bricks. If the storage tank is filled with these, significantly less liquid salt is needed. This is because the salt flows around or through the bricks and gives off its heat of around 560 degrees Celsius to the bricks.
Liquid salt contributes significantly to the costs of high-temperature storage facilities
"Several 10,000 tonnes of liquid salt are needed for larger solar thermal power plant storage. With a price per tonne of currently up to 2,000 euros, salt, together with the two-tank storage systems that have been common up to now, is a considerable cost factor", explains Newcline project manager Christian Odenthal. It can account for up to 50 per cent of the investment costs of the storage tank. The research project aims to change that. Firstly, by using only one tank in which both the cold and the hot liquid salt circulate. This saves heat losses, space and costs for the second tank and the associated infrastructure. Secondly, the researchers are experimenting with a new type of heat-storing filler material in the tank. This would significantly reduce the volume of liquid salt circulating.
High-temperature heat storage tanks could be used in industrial plants in the future
The project partners' desired goal is to reduce the costs to such an extent that the high-temperature heat storage tanks can be used not only in solar thermal power plants. The team of scientists is for instance focusing on process heat in industrial plants. High-temperature heat storage tanks could provide intermediate storage for the process heat in a resource-saving way during times of oversupply before it is used at times of lower supply.
Moulded bricks must be permeable and at the same time form-stable
Newcline is an EU project with a total of five partners from three countries. Besides Germany, Spain and Switzerland are also involved. Each partner takes on certain work packages. The tasks between the two German research partners are clearly divided: The experts at Kraftblock develop and test different material compositions for the heat-storing bricks. These must be form-stable and at the same time permeable so that the liquid salt can flow through them as optimally as possible. Christian Odenthal and his team at DLR, in contrast, are primarily concerned with the question of how the moulded bricks can soon be integrated as optimally as possible into the test tank of the "Test Facility for Thermal Storage in Molten Salt" (TESIS) at the DLR site in Cologne. The first trials are to begin there next year.
"The DLR tank in our large-scale research facility is around 6 metres high. To enable us to fill it with bricks as well as possible, we will use a system of three containers with a lattice floor", Odenthal reports. These are first filled and then placed on top of each other in the round tank. For the geometric shape of the bricks, the partners identified a honeycomb shape as suitable after various tests and with the help of simulation software. This is the easiest to integrate into the round containers.
Liquid salt must not have any residues from the storage materials
The next step will be trials in a furnace to check the production conditions and the quality of the required moulded bricks. This is what is happening in Barcelona. The Universitat Politècnica de Catalunya is another project partner. In addition, liquid salt from earlier laboratory tests at DLR is analysed using wet chemical methods (e.g. ion chromatrography). "It’s important for us that the liquid salt does not have any residues from the fillers", explains Christian Odenthal. "In our TESIS test facility, we have 80 tonnes of expensive liquid salt. This must not be contaminated." (it)