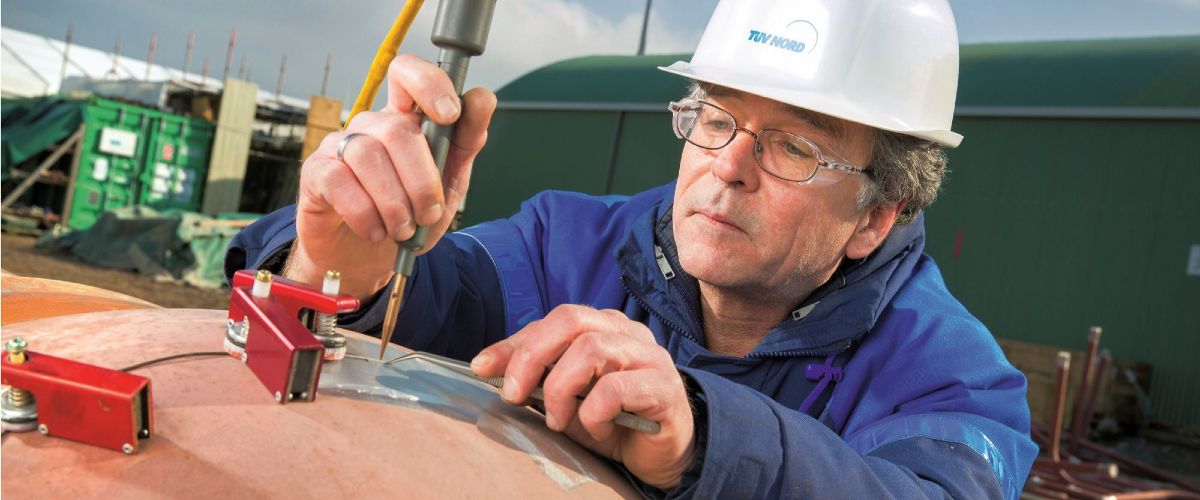
Thermal power plants
Material stress in flexible power plants
The operating conditions for conventional coal and natural gas power plants change considerably when combined with renewable energy sources. In future, they will run more frequently under partial load, have considerably more start-up and shut-down cycles and the components are not loaded as originally designed. Scientists have investigated the thermal and mechanical load of thick-walled components in power plants under the new conditions. The aim is to calculate the stability of components against damage more precisely while maintaining the same level of safety and thus optimise their operating times economically.
Project context
Steam power plants based on coal or natural gas have until now been designed for operating phases that are as constant as possible, with stable temperature and internal pressure conditions. Steam turbines usually operate at 540-600 degrees Celsius and 240-290 bar. A power plant should reach this target range for full load operation as gently as possible and maintain it for a long time.
However, the energy transition requires a much greater flexibility of these power plants. They are closely linked in the grid with wind farms and photovoltaic systems and have to cover the remaining electricity requirement not covered by renewable energy sources as well as most of the system services for grid stability. As a result, these power plants are stressed by frequent starts and transitions to partial load operation. Each time, this means thermal changes of several hundred degrees for the components in comparatively short periods of time.
Research focus
In the THERRI research project, scientists have investigated the loads caused by cyclic temperature changes under the changed load profiles in power plants and developed and tested a new method for fracture mechanical damage tolerance analysis experimentally and numerically. TÜV Nord carried out the project together with the University of Rostock and Forschungszentrum Jülich. The practical tests took place at the KNG power plant Rostock. The load-dependent inspection intervals for the boiler circulating pump and the superheater collector were determined.
Innovation
The results represent a paradigm shift for power plants, because in future the change fatigue of components will be more important for their lifetime than their long-term stability against creep cracks.
Results
The central result is that for the temperature range up to 550 degrees Celsius, the reliability of the applied structural-mechanical investigation method for thick-walled components with curved surfaces was confirmed experimentally, numerically and in practical tests at the Rostock power plant. The concept offers five advantages: It enables components to be used for longer, it contributes to the optimisation of start-up and shut-down processes, it enables flexible inspection intervals and longer inspection periods and it helps to avoid premature replacement of components. Ultrasound investigations have proven to be a successful method for non-destructive material testing, a central component of the concept.
Safety assessment method
So far, the technical codes and regulations for the safety of power plants evaluate the fatigue loads purely computationally and assume the constraints of previous full load operation. If a power plant component exceeds the permissible value of 100 per cent for fatigue, the test conditions become more rigorous. From a certain type of damage onwards, component replacement becomes mandatory. However, these regulations already allow differentiated, in-service inspection methods with an increased extent of non-destructive material tests as an alternative to pure fatigue analysis, as have now been developed in the THERRI partnership.
Practical transfer
The project results allow the remaining lifetime of central plant components to be calculated more accurately for the first time without having to make any concessions in terms of technical safety. These findings are important for the economic evaluation of the power plant operators because the plants generate lower revenues than in full load operation due to the more frequent partial load operation and numerous standstills, whilst also incurring higher servicing and maintenance costs as a result of these load changes. The findings of the investigations were included in a new draft guideline on the "Determination of Inspection Intervals for Thick-walled Power Plant Components by means of a Damage Tolerance Analysis" which was submitted to VGB Power Tech for review and comment.